In August 2023, the slime processing plant of the Donskoy Mining and Processing Plant was launched. Each year, the plant will process about 1.7 million tons of permanently generated waste and, importantly, previously accumulated slime.
The new plant meets all international technology and automation standards. Slime is processed here using gravity concentration method. This method has never been used anywhere else in the world for extraction of chromium oxide from this type of raw materials.
Total investment in the plant amounted to 96 billion tenge. The project is financed with the participation of Kazakhstan Development Bank JSC.
The ERG Green beneficiation plant is one of four projects of the large-scale program for processing of waste slime at the Donskoy Mining and Processing Plant. The project will result in processing of 14.5 million tons of historically accumulated waste.
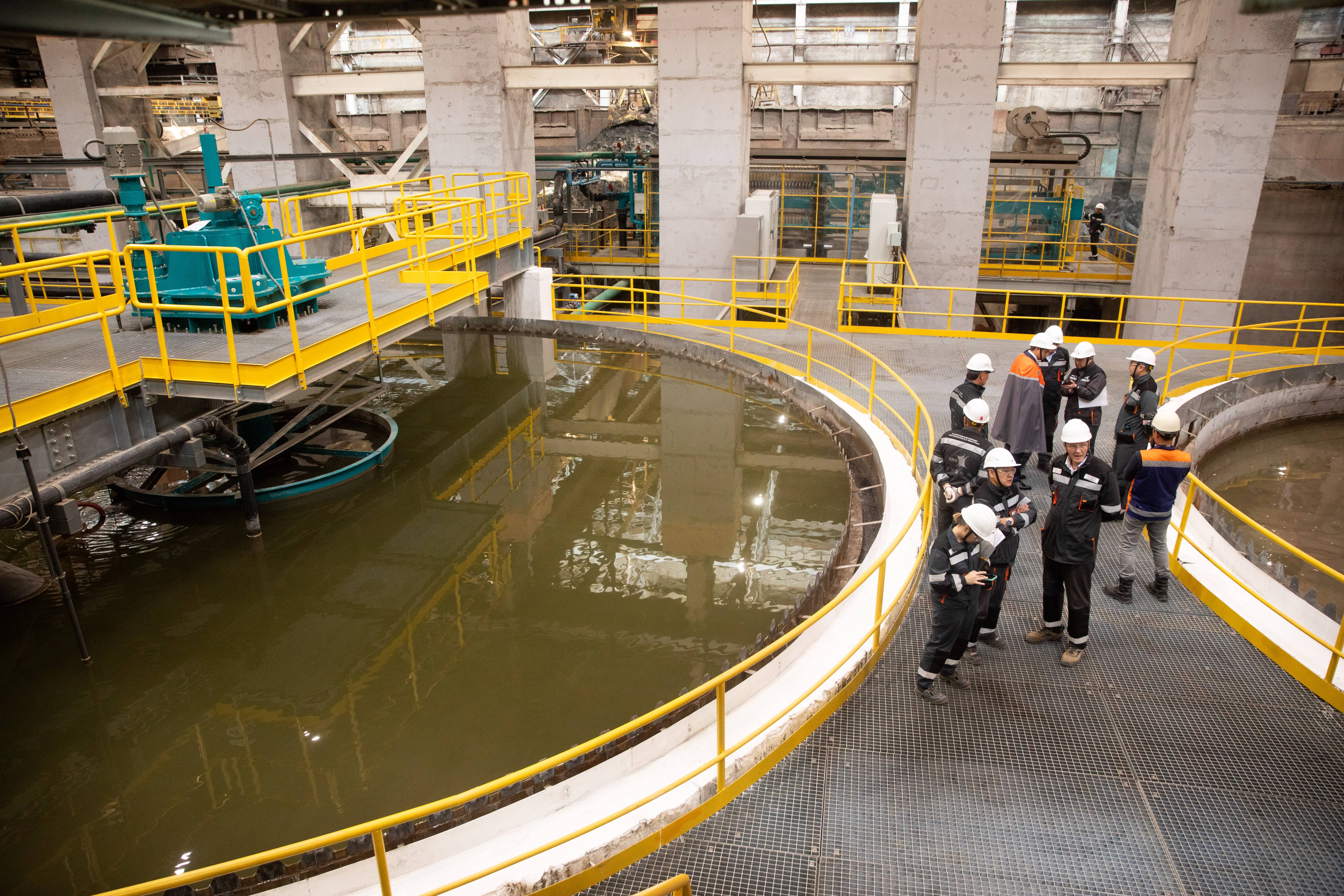